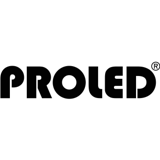
Simplyfying the outgoing goods process by means of a digital workflow
A document-based workflow for outgoing goods, developed by Konica Minolta, is saving LED lighting expert MBN-PROLED at least five to six working hours per week. In addition to the time and cost savings, the company with around 30 employees is also able to impress its customers thanks to the digital storage of documents.
MBN-PROLED sends around 100 shipments of LED lights to national and international customers every day. Up until a few months ago, the associated outgoing goods documents, including logs and packing lists, containing handwritten notes which related for example to batch and serial numbers, were filling up around two to three folders per week. “If a customer or a member of our staff had queries about the deliveries, it took a lot of complex work and time to find the right information in the documents we had stored away,” reported Bernd Menrad, Managing Director of MBN-PROLED, whose aim was to make the company faster and more efficient using process digitisation. “Now any search requires just a single click which enables each employee to see the information they are looking for.”
An automated workflow for digitisation, which is based on a hardware and software package from Konica Minolta, makes this possible. It consists of the Konica Minolta bizhub C558 multifunction system (MFP) for printing, copying and scanning, together with the Nuance AutoStore software solution for recording and managing documents and the dokoni FIND software solution for document searching. At present, with the solution used in daily operations, all outgoing goods documents are scanned as a stack once per day and stored in the digital archive, which employees can access from their workstations at all times.
Expert consultation was the deciding factor
Konica Minolta, which has been a reliable IT hardware supplier of MBN-PROLED for many years, managed to win over the LED lighting expert with this workflow solution in next to no time. “Choosing Konica Minolta was an easy decision for us because the whole process was extremely professional from the very beginning,” Menrad explained. “The Konica Minolta experts knew exactly what they were talking about and what needed to be done. There were none of the vague statements so often made in the preliminary stages of IT projects.”
With regard to the digitisation project, the managing director's primary concern was that the project could be implemented within a short time frame and that the solution would be designed to be automatic and fail-safe. Staff needed to be able to initiate the digitisation process with a single click, without having to navigate through a maze of sub-menus.
After an extremely successful test run with typical MBNPROLED packing documents had taken place at Konica Minolta supervised via a remote desktop session, it was time to develop a detailed plan. “It was obvious that we weren't going to get a plug and play system, but rather a tailor-made solution that met all requirements in full,” Menrad recalled. For example, since packing lists often span multiple pages, the solution needed to automatically detect when a new list would begin and record this as a separate file. This issue was resolved by using a barcode – which can be generated by the project managers using the ERP system – at the start of each packing list.
Almost 100% detection rate
After the bizhub C558 MFP and the required software were installed, the relevant employees carried out a two-week trial after the initial test runs. This resulted in additional minor modifications to the process, such as changes to form fields to ensure optimum positioning of both long and short text entries, e.g. for addresses. “These minor adaptations helped to achieve our current detection rate of almost 100%. Problems can only occur when people make mistakes during operation – for example, when a sheet is sorted upside down,” stated Menrad, who was highly sceptical of whether such a perfect solution was at all possible before the project began.
Now the managing director is pleased that the outgoing goods process has become much more efficient and simple: “We are saving five to six hours of working time per week across all employees and will therefore achieve a return on investment after less than one year, without taking into account the space and costs we have saved for the physical archive.” Menrad also named increased customer satisfaction as another major benefit.
Since everything was also completed as required in the planned time frame and within the allotted budget, Menrad is planning to gradually implement additional digitisation projects within the company.
Challenge
Digitisation of outgoing goods documents
Solution
Custom-designed workflow based on hardware and software components
Advantages
Time and cost savings, as well as increased customer satisfaction
Bernd Menrad
Managing Director, MBN-PROLED
"We received far more positive feedback from customers than we expected – they are happy with our short response times and the ease and speed with which they can obtain information."