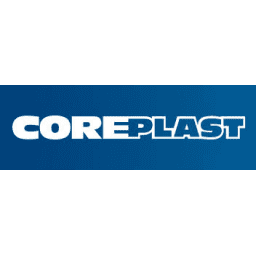
A quality management solution for the preparation, approval round and management of quality documents
Coreplast Laitila Oy, located in southwest Finland, is an important contract manufacturer in the plastics industry. Their services include contract manufacture of injection moulded products, injection moulds, prototype series of injection moulded products, plastic product painting services, plastic product laser marking, ultrasonic welding, assembly services (including ESD), and various printing works (tampo printing, silk screen printing, IML, foil stamping, digital printing).
Coreplast Laitila Oys operations are based on certified quality and environmental systems. These certified quality and environmental systems are audited by both customers and official auditors. The auditors require that the entire change history of an operating manual is trackable from the preparation of a new instruction all the way to its approval. The information should be possible to compile and display in an electronic format, which is why the planning and implementation of collecting log details and an electronic audit trail are of utmost importance. In order to implement this, Coreplast Laitila sought a centralised solution that would support the management of documents created in the quality and environmental system.
High-quality injection-moulded products
The update of the quality documentation follows the standard approval process: author > reviewer > approver. Previously, the company’s quality management documentation was managed in the folder structures of a network drive. The flow of the quality documents’ approval round could not be verified retroactively, meaning there was no audit trail. Each stage of the approval round was missing an electronic signature option, and the manually conducted approval round also required good memory and continuous monitoring.
One solution – many benefits
Konica Minolta supplied Coreplast with the M-Files information management solution, and now the management of quality can be performed in one system. The operating manual and all of its levels were imported into the M-Files system and a hierarchy based on the manual was established between the levels. This makes using the quality documentation easy. Product items were imported from the ERP system into separate target types, which is why all product-related documentation is easy to locate by product item. The customers were also imported into the system as separate target types, which makes it possible to link product items directly to customers, providing direct access to customer-specific information. The current clear and controlled operating model of quality management ensures compliant operations, streamlines work, reduces risks and offers a capability to meet the needs of principals and auditors while securing continued cooperation and improved competitiveness.
Sari Suomistoinen
Quality Manager, Coreplast Laitila Oy, Finland
“I got a strong feeling that we had made the right choice. Switching from the traditional, folder-based structure of managing quality documents on a network drive to the metadata-based M-Files was a big change. Despite the initial challenges, we quickly got the hang of the new system when we started using the solution.”
Quality management uses one overall solution for the preparation, approval round and management of quality documents, such as standard operating procedures, work instructions and auditing guidelines. The solution keeps an electronic usage log in accordance with the quality requirements, which is why deleting or modifying information without leaving a clear trail is not possible. There are several ways to manage the rights to access the quality documents. Access rights can be used to define the file read, edit and deletion rights for the users. In addition, access rights are used to manage the different stages of the quality documents’ lifecycle. For example, production employees can view the work instructions only after they have been published. The solution also includes versioning and an uninterrupted audit trail. The last stage of the approval round—the final approval—applies the electronic signature feature, which also acts as a confirmation of the quality document version that was prepared being ready for publication to the organisation. The approval round workflow incorporates assignments and email reminders to the persons responsible. The implemented solution included automated importing of customer information, product items and product codes in addition to as much other relevant information to M-Files as possible. The solution was implemented as Software as a Service (SaaS).
Collaboration for a successful outcome
Establishing mutual understanding played a key role during the planning and implementation of the solution. In unclear situations, both parties took action to ensure that they reached an understanding. Sari Suomistoinen, Coreplast’s Quality Manager, says: “At first it felt like both parties used terminology that was so different that our discussions were arduous. However, it was great to see that Konica Minolta was genuinely eager to understand our operations and that they worked hard to that effect. Once we got started, I got a strong feeling that we had made the right choice. Switching from the traditional, folder-based structure of managing quality documents on a network drive to the metadata-based M-Files was a big change. Despite the initial challenges, we quickly got the hang of the new system when we started using the solution”, Suomistoinen says.
“M-Files was versatile enough to meet our needs, which was not the case with the other systems that we considered”, says Mikko Toivonen, Coreplast Laitila Oy’s Managing Director. The quality management solution was implemented in 2018, but both parties agreed that this was just the beginning. “We are happy with the cooperation and the benefits gained through the system”, Managing Director Toivonen says. After the implementation of M-Files, the cooperation between Konica Minolta and Coreplast has grown continuously and other projects beyond quality management have been realised.
Advantages
- The implementation of M-Files ensures compliant operations, streamlines work, reduces risks and offers a capability to meet the needs of the principals and auditors while securing continued cooperation and improved competiveness.
- Easy usage of the quality documentation through the establishment of a hierarchy between the levels which are based on the operating manual
- Because of the electronic usage log, deleting or modifying information without leaving a clear trail is not possible anymore
- Manageable access rights to define the file read, edit and deletion rights of the user
- The approval round workflow incorporates assignments and email reminders to the persons responsible
- Automated import of customer information, product items and product codes, which makes it possible to link product items directly to customers, providing direct access to customer-specific information
Challenge
- Looking for a centralised solution which supports the management of documents created in the quality and environmental system
- Improvement of the quality documents’ approval round flow as this could not be verified retroactively
Solution
Implementation of M-Files - Quality Management can be performed in one system
- Versioning and an uninterrupted audit trail to automatically apply the electronic signature feature in the approval round flow